Contributed by Alfredo C.
My Explorer
remains in 4x2, and nothing happened when I tried
4x4 or Low Range buttons. I did all the tests
described in the article, and I concluded that the
problem was the transfer case sensor.
I took apart the whole case. I verified that the
white wheel with the printed circuit (photo 1) had
been unstuck from the central axis. I solved this
problem with some dots of Loctite.

Additionally, I am sending another photo of a
transfer case without the electronic engine showing
the indicators of 4H, 4L, and 2H positions.
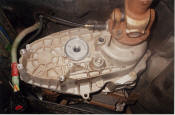
Contributed by J. L.
I just "rebuilt"
the transfer case actuator motor on my '93 Explorer
with 81k miles based on information from that
section of this site. I had the classic symptoms -
push the 4wd button, one click from the back of the
passenger compartment, one more click about 3
seconds later, no engagement. Thanks to your page, I
saw that many others have had exactly the same
problems, so I decided to try to fix it myself. I
thought I'd pass on my observations.
I definitely recommend removing the assembly from
the car, even though that involves cutting the brown
wire. It's much easier to work on the motor and
actuator at a bench with a vise. I also recommend
removing the harmonic balancer assembly - removing
four extra bolts provides much better access to the
motor.
I had to use a dremel to cut slots into the heads
of the proprietary torx screws, which were well
frozen into the actuator housing. I even had the
proprietary 20T torx bit, which promptly became
mangled along with the screw heads, even after I
soaked everything overnight with penetrating oil.
The rubber tubelike stop in my actuator was
completely disintegrated and gone from around the
metal post in the actuator . I replaced it with a
short piece of 5/16" fuel line. It must have been
white - I was finding little pieces of it as I
disassembled the actuator. At first I thought it was
hardened grease or a broken plastic part that may
have been jamming the worm gear, then I realized
based on the little curved pieces that it must have
been what was left of the stop.
With the problems with the proprietary screws, I
had about 5 hours in this job, start to finish. Even
without that problem, working at leisurely pace, I'd
allow 3 hours if you're going to clean up the motor
(armature and brushes, etc.) and get into the inside
of the actuator to check/replace the rubber stop. I
did not approach this as "take off the motor, play
with it a little, bolt it back up, and see if it
works", as some others did to fix problems like
positioning. I wanted to eliminate every possible
cause of failure that I could. When I put it back
together, it worked perfectly!
I jacked up the driver side of the explorer from
the side and supported the frame with jackstands
behind the front wheel and in front of the rear
wheel. That provided plenty of access and headroom -
I would think better than either jacking up the
front or the rear.
Contributed by Jim S.
Based on the
information I found on your site, I was able to
easily repair my '93 automatic Explorer with an
inoperative push-button 4WD control. After carefully
reading the "Transfer Case" page over about six
times, I put the car up on jackstands, pulled the
negative wire on the battery, and got started. I
first unplugged the motor from the wiring harness
(those clips don't *have* to be broken - just push
down on the tab that says "PUSH" and the connector
will come apart with a little effort.)
First, I removed the harmonic damper (the weight
on the left rear of the transfer case). Then I
removed the four bolts holding on the motor assembly
-- three around the round part to the right (where
the position sensing switch wires come out), and one
to the left of the motor housing. As described
above, note the routing of the wires. Remove the
bracket that the main harness connector was
supported by. Notice how it holds the speed sensor
in the transfer case, and holds the wires to the
motor and the position sensing switches up off of
the harmonic damper.
At this point, gentle pulling/wiggling on the
motor assembly will allow you to pull it straight
back and off of the short, cam-shaped shaft that is
hidden behind the round part to the right. As
mentioned above, you will then see that molded into
the transfer case housing are very clear indications
of what direction the narrow end of the cam (the
"pointed" end) should point to for 2H, 4H, and 4L.
Also, so everyone is clear, it appears that there is
a seal around the shaft where it comes out of the
transfer case, so not a drop of fluid is visible.
Everything was clean and dry.
Being the careful sort, at this point I used a
pencil to mark the inside of the motor assembly
where it slides on the shaft: I drew a line where
the "point" of the female receptacle pointed, in
case I rotated it by mistake, so I could re-align
it. I had no intention of turning the shaft (it was
pointing at "2H" when I removed the motor.)
Back to the motor: Three wires will still be
connected to the transfer case. I just lowered the
motor assembly onto a box under the car so I
wouldn't have to splice any wires, and worked under
the car. As described above, remove the bracket from
the bottom of the motor (it is held on by two nuts).
At this point, I wasn't sure just how the motor came
apart, so I'll describe it in more detail than above
for those of you ready to try this fix: The motor
has a rear, flat cover, which is the piece right
under the bracket you just removed. Then there is a
cylindrical piece (with two permanent magnets glued
to the inside), that surrounds the armature. The
front "face" of the motor cover is the remainder of
the assembly. The cover and the cylinder are held in
place by two long bolts, which are actually the same
bolts that hold the bracket on -- once the bracket
is off, you will see two 8-mm hex heads that you
unscrew to open the motor. (These are long bolts
with threaded studs on top -- the bracket was bolted
onto the studs.)
If I do this again, I'll use a marker to mark the
alignment of the end of the motor cover, the
cylinder, and the rest of the assembly before
removing the bolts. (I had to twist them around
until I got the alignment right when I was ready to
reassemble.)
Anyway, I removed the bolts, eased off the cover,
and found that the magnets in the cylinder exert
quite a pull on the armature when you are trying to
remove the cylinder. I wound up removing them
together. Strangely, I don't remember having to turn
the armature to remove it. I must have, though,
because I did not have to rotate the motor to line
up the female slot on the motor assembly with the
shaft on the transfer case when I was done.
The brushes mentioned previously are mounted in a
plastic plate that is part of the rest of the
assembly. I knew from reading above to watch for the
brushes and springs popping out, so I removed the
armature very slowly. Not that you know right where
the brushes are, you can look in the crack between
the cylinder and the rest of the assembly as you
remove the armature and you'll be able to identify
the brushes easily and watch for those springs to
pop out.
The contacts on the armature were filthy black,
which seemed to me to verify that what the others
above said was true -- they just needed cleaning to
work again.
After cleaning as described by others (I also
used Qtips to clean all the black bits of dust out
of the brush holders, etc.) I was able to put in the
springs and brushes one at a time (there are two)
and hold them retracted as I started to replace the
armature. The copper wires from the side of the
brushes protrude out the slots in the brush guides -
this will be clear once you see it. As I tried to
replace the armature, it wouldn't just push in...
now what? Oh, yes, turn it (the end is threaded;
it's a worm gear). Nothing. After looking again, I
saw it was a *left-hand* thread, so you have to turn
it counterclockwise to reinsert it. Went right in,
no problem.
At this point, I could carefully hold the
armature in place and turn it each way, and verify
that the female slot was oriented correctly to slide
back on the transfer case, since I had marked it on
removal.
Then I just slid the cylinder back on (pushing on
the end of the armature so it wouldn't pull out and
pop the brushes out), put on the rear cover,
inserted the bolts and wiggled them to find the
holes at the other end, and reassembled the whole
thing.
I debated trying to run the motor while I had it
off the transfer case, but decided that I might slip
up and damage some of the other components, and
since it seemed that the contacts were filthy, and I
had them cleaned, I just decided to gamble, so I
reassembled everything, reconnected the battery,
dropped the car, crossed my fingers, and tried it
out.
Everything seems to work perfectly!!
I don't know how long it will last, but my
sincere appreciation to those of you who took the
time to write all the text above: you helped me save
about $450 (what a friend with another Explorer just
paid last year for a new motor). I offer these notes
to perhaps give someone else a few more details, and
give you the confidence to try this repair yourself.
Comments from Tom J.
All of the things
posted are true and correct and one other thing
before they go and replace the motor is that the
contacts on the armature get dirty after much use
and are very easy to clean by taking the two screws
out of the motor and pulling it apart. Care must be
taken and don't lose the two load springs to the
Brushes. Use very fine emery cloth on the contacts
where the Brushes ride. The armature screws back
into the switch housing and care must be taken to
make the brushes clear until they are riding on the
armature. I restate that care must be taken when
removing and replacing the armature with the brushes
and load springs for there is to hold back hole to
keep the brushes from slipping out of their guide.
If you are poor as some of this Oklahoma dirt as I
am and can walk and chew gum at the same time I am
sure that you will find that this will save you the
cost of replacing the motor or having it rebuilt.
Contributed by Greg D.
My third visit to
the 4wd shift motor to remedy a no-shift condition
over the six years and almost 200K miles was greatly
helped by the info submitted by previous
contributors. Here are a few things I learned:
1. The multi-pin connector can be disassembled,
eliminating the need to cut the wire permanently
attached to the transfer case. Just get some needle
nose pliers or large hemostats (is any toolbox
complete without them?) and carefully pull the red
center piece out of the male end of the plug. Then,
gently pry the plastic retainer away from the wire
you want (not too far!). To remove, pull the wire
out the back of the connector.
2. Mark the location of the round plate with the
wires going into the switch housing so you can
reassemble it into the same position when you're
finished. Use a good pair of vice grips to loosen
the small screws with the proprietary head which
hold the round plate to the switch housing. I
replaced mine when reassembling with 8-32 screws cut
to fit. Be sure to use star lockwashers on the
screws, since a good mechanical and electrical
connection is needed here!
3. The round body of the motor itself comes apart
in three pieces. Once the long motor bolts come out,
pull the motor apart. Yes, the brushes and the
springs immediately fall out of their holders, but
getting them back in is easy. After cleaning up the
part of the motor where the brushes ride (use fine
sand paper or an emery board), hold both of the
brushes against their springs, and insert the motor
armature shaft into the housing. Then, slide the
round motor housing over the shaft while holding the
shaft/brushes in place with your finger by reaching
down into the motor body and preventing the magnetic
force from pulling it out. Then, install the end cap
of the motor and reinstall those long bolts.
4. To test the motor, leave the large round
driven gear out of the switch housing, and hook the
wires up as described by drbob, and watch the motor
hum along wonderfully. Reverse the leads, and watch
it go in reverse. After you're finished feeling good
about the motor running so well, lubricate the worm
gear, and the teeth on the driven gear. Slide the
driven gear in and it will engage the worm gear. Run
the motor to one of the stops and reassemble the
cover plate to the position you previously marked.
Well that's it. So far, no problem with the fix.
I had previously tried other fixes, but really
believe that the dirty contacts where the brushes
ride inside the motor were the real problem.
Contributed by Richard F.
I was having some
trouble with my 1991 Ford Explorer transfer case and
talked with a service tech up hear in Alaska about
it. He told me about a test you can perform to the
processor board that is located in the rear left
access panel next to the jack and rear windshield
washer container. In has 2- wire harness pin
connectors attached to it on the left side. If you
remove the 2- wire harness pin connectors and turn
on your ignition switch. Now you can push the white
square button on the bottom edge of the processor
board and it will turn on a red LED right next to
the button. If the red light flashes this means you
have a problem with your actuator motor assembly. If
the red light stays bright this means you have a
problem with the processor board. I found a problem
with a the actuator motor assembly. I followed the
instruction from your web page on Transfer case
problems. I found it helpful but would like to add
some info to it. I didn't need to remove the
harmonic balancer nor drain the fluid. The 4 bolts
that hold the actuator to the case were removed, the
magnetic pickup sensor and I cut the one brown wire
going into the case. I opened up the actuator and
removed the armature. Cleaned it up with some 400
grit carborundom paper and washed it down with some
CRC contact cleaner. I pull the brush holder springs
out and put a little more tension on them because
they seemed to only apply a little tension to the
brushes that were worn to a length of about 1/4". I
polished up the armature shaft where it comes in
contact with the bronze oil impregnated bushing with
the 400 grit carborundom paper. I install some
graphite grease on the worm drive shaft and gear and
bushing surfaces. I installed some RTV sealant on
the cork gaskets before assembling. I removed the 3
-8/32 X1/2 " anti-theft screws on the gear cover and
cleaned the face of the gear with the foil trace
circuits on it and the 5 copper contact surfaces on
the cover with CRC contact cleaner and 400 grit
paper. I used some RTV sealant on the cork gasket
before installing the cover. I also installed some
RTV sealant on the 5 wires that go through the cover
rubber grommets that don't do a good job at keeping
out the fine dust that was found on the contact
surfaces within. This I feel is the root of the
problem! Now I cleaned up the transfer case and
actuator surface where it meets the case and
installed some ATV sealant on it and bolted it back
together. I install a #14-16 pin connector male and
female on the wire I cut and put some heat shrink
tubing over it to seal it up. After 1 hour of
tinkering I am back on the road. Wala- a simple push
of the button and I was in 4 wheel drive again. The
first snowfall in Alaska this year has now come and
I am ready for it. With 4 studded tires I can drive
on the glacier roads at 55MPH and feel safe.
Contributed by Chad C.
I have a 1993 Ford
Explorer and I was not able to shift into 4-wheel
using the push button today. I thought that Ford
might have a page that I could use to start to
trouble shoot from. Accidentially, I came across
your page and read the tranfer case section. Using
that information I started at 10:30 tonight and now
at 12:00 A.M. I just finished my test drive and
everything is working great. You may want to add
the following to your page. When troubleshooting a
push-button problem use the following steps before
removing the motor. 1. Using a VOM
(Volts-Ohm-Meter) test continuity between pins 10, 6
and 8 (2-Wheel). To determine others 4L, 4H
refernance previous sections. If you have
continuity the brushes and armature need to be
cleaned in the motor. If not you can move the
motor +/- 15 degrees that should produce
the continuity you need. In my case I did have
continuity, so I removed the motor cleaned the
armature and brushes.
Contributed by Jim B.
With the harmonic
damper removed and all 4 motor mounting screws
removed, remove motor and then slip back over the
indicator cam. If 3 bolt holes on main body line up
with holes in transfer case then motor position is
in line, otherwise it's off.
With motor removed from transfer case, mine would
only attempt to turn 5 or 10 degrees when engaged.
Went to Auto Zone and bought a set of "tamper proof
bolt" torx bits ( cost $17 ). Took off round cover
and removed cam gear. Small piece of tubing ( which
is a stop ) was badly worn. Also contacts on cam
face were dirty. Cleaned contact and used a small
piece of 5/16 fuel line for stop. Reassembled and
works perfectly!
Contributed by Gerry S.
I would like to
commend on this site for it saved me $$$. I had a
similar situation in the "Fixing the Transfer Case"
section. I recently had my transmission rebuilt on
my 93' Explorer. Shortly afterwards, I noticed the
4X4 wasn't working. No lights, no sounds, when
pressing the button. I figured that when they
rebuilt my transmission they forgot to hook
something up. I took it back and it sat in their
shop for 2 days before determining everything was
hooked up and it was nothing that they did. They did
say to take it to the dealership and if they were
found at fault they would flip the bill. I took it
to the dealership. They called me a couple hours
later and told me they need some more time to
diagnose the problem that it wasn't something simple
like the switch or fuse and I authorized the extra
hour for troubleshooting. They called me the next
day and told me it was the shift control module and
the total bill would be $700 parts & labor. I wasn't
going to authorize anything over the phone so I did
some researching. I found your site and read it over
a few times. I went down to the dealer a little more
knowledgeable than before and questioned their
techniques and pricing for this job. I asked to see
the service manual and time breakdown. I must have
won the argument as I left the dealership without
paying a dime, but I still have an inoperative 4X4.
Following your instructions, I was able to find the
problem (limit switches) and fix the problem myself
in less than an hour.
I would like to add comments though:
I would completely remove the shift motor/switch
controller for ease of cleaning the brushes and
switches. It is a simple process to take the 3
permanently fixed wires to speed sensor out of the
wire connector. This can be done by removing the
yellow "lock ring" out of the center of the plug and
pressing back on the plastic tabs on the pin for the
wire you want to remove.
Cleaning the motor brushes and commutator is
straight forward. Putting back the armature was a
little difficult with the brushes in place, as I
didn't have any extra hands. My tip: use wire ties
or something similar to hold brushes in place while
replacing the armature in housing then cut them off.
Make sure you mark the switch cover before
removing. I found removing the cover required a
special torx bit, which I didn't have. I had to
punch out the center of the bolt to remove that
piece that was preventing me from using my regular
torx bit.
Contributed by Glen S.
We just completed
the "Transfer Case Motor Brush Cleaning" outlined in
your FAQ. The information was incredibly valuable,
especially the comments in Jim Schneider's section.
To make the repair even easier we have a few
comments to add (all for a '91 Explorer 4x4):
1) Harmonic Balancer Removal is NOT necessary (at
least on a '91 Explorer) Although Jim Schneider and
others suggested this removal, we sucessfully
detached & reinstalled the motor assembly WITH the
balancer in place without any hinderance. In other
words, removing 4 bolts and disconnecting 1
connector is all that's needed to remove the motor.
2) 10 pin harness disconnects without damage
Although incredibly deceiving, the tabs on this
connecter must be pushed DOWN to disconnect rather
than pulled up as it initially appears. The tabs
have a thin slot, so that when the tabs are pushed
down the slot sneaks UNDER the knob (which is T
shaped in cross section). It sounds confusing, but
will make much more sense when looking at it.
Reconnecting is made easier by lightly widening the
thin 'tab slot' with sandpaper.
3) Motor dissection and brush cleaning easier
than it sounds The only tricky part, which is
greatly aided by an additional set of hands, is
pushing the brushes outwards while installing the
armature. Still not tough, but might take a few
tries. The only thing to lose is the two springs,
but they stay in place rather well and the brushes
are attaced by wires.
4) In the big picture, it seems that there are
several repair procedures depending on your
situation a) Motor Brush Cleaning (we did this) b)
Motor Alignment (even after completing "a" we still
don't see where there enough play in the motor
mounting to allow varying the alignment) c) Motor
Position Sensor Debugging (ie. checking the
continuity of various pins combinations on the 10pin
harness) d) Shift Computer Reset (press little white
button on controller inside truck above left-rear
wheelwell) e) Other more insiduous problems
And this exchange found in my
inbox
From Michael T.
My system does the following: pressing the dash
button causes a short series of clicking noises at
the back of the vehicle, but nothing else happens.
I've not taken mine in to be looked at. Have you?
From Barry N.:
Mine had the same problem - read on in the
cut/paste below (especially the URL and my
experience here relates only to the electric motor
on the t-case and assumes you have no problems with
your hubs, 4WD computer controller or other related
components).
I'm not sure how familiar you are with this so
I'll go through it as much as I understand it. There
is a little electric motor on the transfer case
(similar to ones used on electric windows) that is
used to engage the 4WD and as Dr. Bob explains,
there are a lot of things that can happen with it.
Mine hadn't worked for quite some time but after
fooling with it and somehow getting it to work
intermittently, I decided to have my mechanic look
at it. First he took the motor out by unplugging the
connectors and cutting the red wire that's hard
wired in. Then he took the cover to the motor off
with a safety torque tool (why they would want to
keep people from being able to take this motor apart
is one of the many roadblocks Ford likes to throw in
our way). Then he took some fine steel wool and
cleaned up the contact surface. When he removed the
contact surface, there was a very short piece of
plastic tubing serving some purpose (I can't
remember exactly what) but this had practically
disintegrated. He just replaced this with a piece of
rubber tubing and we were onto putting 12V to it (be
careful here as Dr.Bob says) and it worked fine, put
it back together and its still working today.
Comments from Hubertus
Tried your cure
for the transfer case problem described in your
maintenance note. The symptoms were identical to the
ones described: only a faint double click from the
controller, but no action. I removed the control
motor, turned the selector cam a few times and
replaced the motor. Everything worked fine
afterwards! However beware, this may not be a
final fix!
I took the car on a desert tour through the Namib
Desert in Namibia two weeks later. Surely after
working without a hitch for almost three weeks, the
problem reoccurred in the middle of a sand dune
field and could not be fixed using the prescribed
procedure. Only almost totally deflated tires and
courageous driving in the 2wd mode saved me!
Comments by Gary P.
Be sure to mark
everything before disassembly so that it will go
back together as it was. Especially the little
cover plate for the switch contacts. They must go
back to the original position so that the timing is
correct. If not for this site, I would have
probably gone to Ford for the $400 fix. Instead I
Instead I did it myself, as the others did, for
free.
Notes from a Happy Customer
Living in New
England, the weather can quickly bring winter snows
upon us. I have a 1992 Explorer with the electric
transfer case. Two days ago, during our first (6
inches in 3 hours) winter storm, my wife and I had
to go out for the evening. We took the Explorer
because we needed the four-wheel drive to get
around. You can imagine the disappointment when
repeated pushing/pounding/cajoling of the buttons
produced no result. We made it through the evening
barely but came home "very" concerned about the
reason for not having the four-wheel drive.
Yesterday morning, I decided to have a look on
the NET to see if there was anything available with
technical guidance. Ford does not have a TSB on the
problem, so I looked for other information and found
your site. The article on fixing the Transfer Case
described exactly what had happened to me. I decided
to call my local garage anyway to have the vehicle
checked out. They immediately told me it was the
motor (having replaced several for other owners) and
the cost to replace it would be in the range of
$400. I then called the Parts Counter of my local
dealer to see if they had any in stock because the
instructions in your article make the change out
seem quite easy. The dealer had 12 in stock (I can't
imagine why) and indicated they could change it
early next week. Price was $250 for the part but
they had it on sale for $189.
I picked up the motor just in case and went home
to work on the Explorer. Starting at 7:15, I rolled
it up on the ramps, pulled the balance wheel,
unhooked the electrical connector (the tabs are
supposed to break off aren't they?) and pulled the
motor off of the transfer case. I took a screwdriver
and rotated the motor slightly counterclockwise and
with my trust 8-year-old daughter in the driver's
seat, determined that the motor was now working
fine. Slapping it back in was a breeze and I was
back in business. The vehicle was back down off of
the ramps at 8:15 completely operational. Total cost
$0.00. Tools required: 13mm, 11mm socket, pliers,
screwdriver, 2 band aids (for me) and one assistant
to push the buttons ensuring the motor continued to
function during the fitup.
It is interesting that neither my mechanic nor
the dealer even hinted that adjustment might solve
the problem. Both were very willing to toss the
original motor and install a new one. Your article
saved me $200 for a do-it-yourself job and $400 for
a neighborhood mechanic. I was afraid to ask what
the dealer would have charged. Maybe Ford should
consult you for a future TSB issue.
Another Testimonial from Russell
S.
A few weeks ago, I
had trouble with the electronic 4X4 shift on my 1994
Ford Explorer. I was about to change the shift motor
until I found out the cost. Retail it was over
$300.00 and wholesale it was just under $200.00.
That changed my mind on just a simple parts change
out. I got under the Explore and was going to do a
simple continuity check of the motor only to find
out that there were not two or three wires in the
wiring harness, but 10. Without a detailed wiring
diagram, I had no idea which wire went where. A
couple of nights later, I was surfing on the Net and
came across your site and your explanation about the
motor losing its neutral reference. The next
Saturday I went out to try your fix. I found the
motor was indeed about 15 degrees off when the unit
was in two-wheel drive. I tried to turn the motor
with a large screwdriver, but I could see that the
gearing was working against me. Not wanting to admit
defeat, I pulled the end cap off the motor and
rotated the armature until the motor mounting bolt
holes lined up with the shifter when the unit was in
2 wheel drive. I put everything back together and
just knew that I had fixed the unit, only to find
out that I still had no shifting.
The next weekend I took the Explorer into my
local Ford Dealer to have the warranty work on the
remote mirrors taken care of. While I was in there,
I asked if they had a wiring diagram I could look
at. They were nice enough to furnish me one. I
looked it over and thought that maybe I had a wiring
or switch problem. I pulled small door off the
inside of the left rear wheel well and started to
check the wiring. The controller is the top one of
the two in this location. Prior to starting the
wiring/switch troubleshooting, I pulled the negative
battery terminal of the battery. Two of the
connectors to the controller are easy to get at so I
checked them first. Everything checked out OK on
those two. You can check the neutral safety switch,
the shift buttons and some of the other wiring. The
other connector requires the removal of the whole
interior panel, or a lot smaller hands than I have.
After checking the first two connectors, I decided
to put things back together and wait for another day
to take out the whole interior panel. I hooked that
battery back up and started the engine to make sure
everything was OK. Out of desperation, I checked the
shift buttons and found everything working. The only
thing I can figure is that when you re-center the
motor, you have to disconnect and reconnect the
battery so the controller can reestablish its center
location.
The unit still works just fine after about a
month. I've told my wife not to shift on the go, but
to stop and shift. I'm not sure that relates to the
problem, but since it was new it has made a bang
when some of time when you shift out of four-wheel
drive on the go. Two things I would never order on a
new vehicle again are electric shift and antilock
brakes.
Thanks for your help. I fixed the unit for $0.00
instead of $300.00 plus.
Contributed by Micheal C.
Having the same
familiar problem with the four wheel drive transfer
case motor (push the 4x4 button, hear a few clicks
from the drive side rear wheel, then nothing) so
after reading your site decided to try fixing it
myself. The whole job took about two hours.
I took the advice of one of your contributors and
didn't cut the brown wire. The wire can be easily
remove, as he said, from the harness by removing the
red center ring with needle nose pliers. Once the
ring is removed gently insert a small thin
screwdriver between the black tab and the brown wire
pin and pull on the wire from the back of the
harness. I also did this with the green and blue
wires from the transfer case sensor. Wasn't sure how
the sensor came out of the transfer case, pull on it
a little but it wasn't moving, though it best just
to remove the wires from the harness. (Just write
down the color of the wires they're next to so you
can reinsert them correctly).
Before I disassemble the motor I mark the casing
in various spots to make sure every was put back
together correctly. I found the plastic stop in 3
pieces (looks like harden yellow grease) I cut a
piece of rubber tubing and place this over the screw
like stop on the actuator. I wash down all the
electrical components with contact cleaner and used
Qtips to wipe away the residue. Reassemble was a
little difficult because of the brushes but I did
get it together after a few tries.
I didn't remove the harmonic balancer at first
but couldn't get the motor to line up on the
transfer case. Once the balancer was removed the
motor slipped easily in place. Took the car for a
test spin, press the button and presto, I have my
four wheel drive back. The only things I can
recommend that before you start this job. Pick up 3
(8x32) bolts to replace those stupid torx screws
(easily removed with vise grips), CRC electrical
contact cleaners and RTV silicon gasket cement.
Contributed by Clark B.
I have one piece
of advice to add. The site explains very well how to
clean the motor once it is off and how to reinstall,
but little is told about taking it off and which end
of the motor to remove first.
1) After removing the motor and unclipping the
wire harness there are three wires left. Two wires
go into a small magnetic sensor to the far right of
the motor and just to the left of the brown wire.
This sensor comes out, but you must pull it out. Its
not screwed in but is held in place by a small
rubber ring. Simply pull straight back and it will
come out.
2) When removing the motor's end cap (the part
that looks like a cola can, not the circular part
with wires going inside), you must pull straight
back. Mine had a worn adhesive ring around both caps
(one on either end of the 'can'). I removed the nuts
holding the metal piece that attaches to the
transfer case then removed the two long screws.
>From that same end, I forced the cap off.
Apparently when removed the cap came off at an
angle. DO NOT REMOVE THIS END! This cap has a 1 inch
washer held in place by 6 very brittle metal tabs.
Three of the tabs broke either on there own or from
the angle of removal. The small 1 inch nut now roams
free in my electric motor and you can hear it
rattling when engaging or disengaging. I plan to buy
a similar washer and put both on, this will force
the 1 inch washer into the cap thus stabilizing the
worm gear. This is very important, if I had removed
the end cap which is attached to the round housing
with wires, it would have come off straight and not
broken these tabs. Be very careful.
Contributed by Joe M.
I also had a 4X4
select problem, no response at all. Thanks to your
website it was easy to cure the problem. I would
like to share my experience. Mine occured at about
95,000 miles on a 1994 Ford Explorer Limited. About
the only time I use 4X4 is retrieving my boat from a
steep slippery ramp.
I read every contribution several times, and
especially appreciated having the knowledge how to
disassemble the 10 pin connector at the motor
without cutting the brown electric clutch wire.
I have a couple of items to contribute. I also
agree the brush carbon buildup on the armature is
the root cause of the problem since I could not get
the motor to move in either direction when applying
power directly to the motor 10pin connector prior to
removing the motor assembly.
After disassembly and cleaning the armature, use
a couple of rubber bands to hold the brushes in
place until the armature is reinserted. Then simply
cut them off.
Disassembly of the speed sensor also revealed a
disintegrated nylon bumper. I used 3/8"OD X 1/4"ID
poly water line, it was a bit snug on the bumper
screw, but matched the dimensions of the
disintegrated bumper closer than 5/16" gas line. It
was also necessary to burnish the inside case die
cast patterns that protruded enough to possibly snag
the nylon bumper.
I do feel that Ford misaligned the Shift Position
Sensor assembly too close to the 2wd endstop during
manufacture. This caused the bumper to disintegrate
as it was forced against the 2wd stop. This then
contributed to the excessive carbon buildup on the
armature since the motor is still trying to go past
the end stop.
I moved the Shift Position Sensor about 5 degrees
Counter Clockwise away from the 2wd end stop,
reinserted the motor assembly on the selectorshaft,
then turned the selector shaft clockwise until the
motor mount holes matched the transfer case bolt
holes. The result is the motor will no longer jam up
against the 2wd endstop.
A second problem I had was the rear ABS warning
light came on. The cause of that problem is the rear
speed sensor mounted on top of the rear differential
assembly. This must be a high failure item because I
found the same problem on my son's 1994 Ford F150.
Contributed by Chris H.
I went through
this problem of repairing the shift motor on the
transfer case on 91 Explorer. One post here mentions
that you need to cut the brown wire leading directly
into the transfer case to seperate the motor from
the transfer case. DO NOT DO THIS! I have the Ford
Manual and there is a much simpler way to do this,
and you will not be risking a loose connection where
you splice the wires back together.
When you unplug the wire harness from the shift
motor, look into the motor side of the harness. You
will see a little circle of plastic surrounding the
center pin.(Red in color on my truck but I can't
guarentee it's always going to be red) Fashion a
tool to pull this plastic piece out: straighten out
a paper clip. Make a 90 Degree bend at one end
forming a tiny hook. The bent part should only be
about 1 mm or the thickness of a dime. Using this
hook pull out the red plastic piece from the center
of the large black pulg. Don't lose it. This plastic
piece locks all the pins in place. Once the red
piece is out, release the tab on the center pin of
the plug(the brown wire) with a small screwdriver or
pick and pull the wire out of the back of the wire
harness. Now the brown wire is seperated, and you
can remove the shift motor from the transfer case
without cutting wires.
Contributed by Ed & M.
Having the same
familiar problem with the four wheel drive transfer
case motor not operating I followed most of the
previous efforts fairly close. The brushes looked
good, the copper looked fine, the nylon
washer/bushing was beat up so I replaced it with a
1/4 inch piece of gas line with the same inner and
outer diameter. (I wondered why I had kept that
piece of gas line.) Relubed the gear checked the
motor with 12 volts from the battery and it worked
great either way. Installed on the transfer case and
drove it off the ramps. Successfully went into 4x4.
Took several efforts to get it to disengage. Then I
had the same problem as before I started. Light in
back blinked. Motor didn't function. Crap. The next
weekend took 12 volts and motor did not work. Took
motor off the case and the motor worked. Put it on
and it didn't work. Looked for pinched wires or any
other thing that could cause this. No joy. Removed
motor. It worked. Reinstalled and it didn't. Backed
off the bolts and it worked. Tightend and it didn't.
Removed motor installed thin washers and almond
colored rtv (it has to be almond) between motor and
case and tighted it up and it works fine. 4x2, 4x4
and 4x4 low. Will take it to the desert tomorrow for
final checkout.
|